
Rekordbox vs Serato – Why Not Both? Introducing The Pioneer DJ DDJ-GRV6
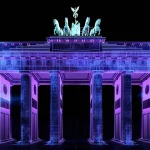
MadMapper vs Resolume: Which Projection Mapping Software Is Better?

Rekordbox vs Serato – Why Not Both? Introducing The Pioneer DJ DDJ-GRV6
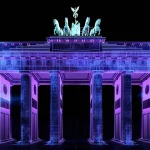
MadMapper vs Resolume: Which Projection Mapping Software Is Better?
What is Aluminum Alloy? Understanding Markings for Truss and Stage Safety
Introduction
What is aluminum alloy, and why are aluminum markings essential in truss and stage systems? Aluminum alloys, valued for their lightweight strength and corrosion resistance, are crucial components in staging. Yet, not all aluminum alloys are the same. Markings on aluminum products provide essential information about alloy type, tempering, and certifications, and each of these factors impacts the alloy’s suitability for demanding applications. Thus, this guide offers truss professionals a comprehensive reference to aluminum alloy markings, helping them choose materials that meet exact standards for strength, durability, and compliance.
Aluminum Alloy Series and Usage
The aluminum alloy series designates the main alloying elements added to aluminum. These elements impact the alloy’s strength, weldability, and corrosion resistance. To help navigate these differences, here is a table that outlines specific aluminum alloy markings, temper designations, and practical uses for truss systems.This table provides a reference to specific properties of common aluminum alloys used in truss applications. By referring to it, industry professionals can understand which alloy type best suits their needs.
How Alloy Series and Temper Markings Affect Truss Performance
Aluminum alloy series and temper markings reveal important information about how each alloy performs in real-world applications. Below, we’ll examine two popular alloy series used in trusses and explain how they differ.
6000 Series Aluminum Alloys
The 6000 series combines magnesium and silicon to balance strength, corrosion resistance, and weldability. Markings like T6 temper mean the alloy has undergone solution heat treatment and artificial aging. These processes increase durability, making the 6000 series a practical choice for truss applications.
6000 Series Aluminum Alloys
On the other hand, 7000 series alloys primarily contain zinc, with the T651 temper adding extra toughness through controlled stretching. While this series provides significant strength, it’s more common in aerospace applications due to its cost and lower corrosion resistance compared to the 6000 series.
Certification Standards for Aluminum Markings in Trusses
ASTM Standards and ISO Certifications for Aluminum
When choosing aluminum alloys for trusses, it’s crucial to know which standards ensure quality and reliability.
ASTM Standards for Aluminum Markings: ASTM standards specify properties like tensile strength and durability, ensuring consistent material quality. Aluminum alloys in ground support systems must meet ASTM requirements to handle high-stress loads safely.
ISO Certifications: The ISO 9001 certification confirms a manufacturer’s quality management practices. This certification does not certify individual product properties directly but guarantees adherence to quality standards.
TÜV Certifications for Truss Systems: TÜV SÜD, TÜV Rheinland, and TÜV NORD
TÜV SÜD and TÜV Rheinland: Ensuring Safety and Durability
Both TÜV SÜD and TÜV Rheinland are respected for conducting rigorous testing and issuing certifications in Europe:
TÜV SÜD focuses on industrial safety and performance, ensuring that products meet high standards for reliability and durability.
TÜV Rheinland specializes in environmental and digital safety, providing valuable certifications for products that face challenging environmental factors or digital compliance needs.
TÜV NORD: The Importance of EN1090-3 Certification for Aluminum Trusses
TÜV NORD certifies both materials and manufacturing processes, ensuring European compliance. Its EN1090-3 certification is especially relevant for aluminum trusses, as it verifies that materials and production processes meet high safety standards. TÜV NORD certification makes GTR Truss products trusted in demanding event environments, as it confirms consistent manufacturing quality and material reliability.
GTR Truss Certification and Marking Details Explained
GTR Truss products use EN AW 6082-T6, a high-strength aluminum alloy ideal for load-bearing trusses. This alloy provides high weldability, corrosion resistance, and durability, making it suitable for heavy-duty stages and outdoor applications. Moreover, the EN1090-3 certification from TÜV NORD guarantees that GTR Truss products meet strict standards for manufacturing and materials, giving professionals confidence in product quality and performance.
How Corrosion Resistance in Aluminum Alloy Series Benefits Truss Selection
Selecting the right alloy for outdoor setups involves understanding each series’ corrosion resistance. Aluminum alloys in the 5000 and 6000 series offer inherent resistance, making them ideal for outdoor staging.
Although no specific “corrosion resistance markings” exist, selecting alloys from these series provides natural protection against corrosion.
5000 series alloys, which are high in magnesium, perform well in coastal environments.
6000 series alloys balance corrosion resistance with strength, making them ideal for outdoor stage packages.
Understanding Load-Bearing Capacities in Trusses and Stages
Manufacturers specify load-bearing capacities in product documentation rather than marking them on the alloy. The load-bearing strength of a truss depends on alloy, welding, and design. For stage trusses, these specifications help determine if the structure can support heavy lighting and equipment safely.
Protective Aluminum Road Cases: Durability and Impact Standards
How Aluminum Markings Ensure Road Case Durability
Aluminum road cases don’t have “impact markings” but typically come with certifications or testing results to verify durability. These certifications ensure that cases like those in GTR Direct’s selection can handle the demands of frequent handling, making them ideal for transporting audio and DJ equipment.
Additional Considerations for Industry Professionals
Compliance with ANSI and EN Standards for Aluminum Markings
Adherence to ANSI E1.2 (for aluminum trusses in entertainment) and EN1090-3 is critical in staging applications. ANSI E1.2 confirms structural safety, while EN1090-3, certified by TÜV NORD, validates manufacturing consistency and material standards.
The Role of Heat Treatment in Aluminum Alloy Properties
Heat treatment plays a significant role in aluminum alloy strength and flexibility. Designations like T6 and T5 show specific treatments that increase strength and corrosion resistance. T6 temper is durable and ideal for load-bearing trusses.
Choosing Aluminum Alloys for Welding and Outdoor Use
The 6000 series alloys weld well, making them ideal for truss construction. Additionally, 5000 and 6000 series alloys withstand humid and marine conditions effectively, which makes them suitable for outdoor setups.
conclusion
Understanding aluminum alloy markings, temper designations, and certifications helps truss professionals choose materials that meet rigorous safety and durability standards. TÜV NORD’s EN1090-3 certification, in particular, supports well-informed decisions, ensuring long-lasting, dependable performance in staging and protective applications.